Инструкция По Визуальному И Измерительному Контролю
- Инструкция По Визуальному И Измерительному Контролю Скачать Бесплатно
- Руководящий Документ. Инструкция По Визуальному И Измерительному Контролю
Постановление Госгортехнадзора РФ от 11 июня 2003 г. N 92 “Об утверждении “Инструкции по визуальному и измерительному контролю” Госгортехнадзор России постановляет:.
И измерительному контролю. По визуальному и измерительному. Настоящая инструкция. Руководящий документ инструкция по визуальному и измерительному контролю. Визуальный и измерительный контроль (ВИК) — Один из разновидностей методов неразрушающего контроля, в первую очередь основан на возможностях зрения, объект контроля исследуется в видимом излучении. Метод проводится с использованием простейших измерительных средств таких как: лупа, рулетка, УШС, штангенциркуль и т. С его помощью можно обнаружить: коррозионные поражения, трещины, изъяны материала и обработки поверхности и пр. Также проводят при помощи оптических приборов, что позволяет значительно. ИНСТРУКЦИЯ ПО ВИЗУАЛЬНОМУ И ИЗМЕРИТЕЛЬНОМУ КОНТРОЛЮ ИНСТРУКЦИЯ МИНИСТЕРСТВО ТОПЛИВА И ЭНЕРГЕТИКИ РФ 15 августа 1996.
Утвердить “Инструкцию по визуальному и измерительному контролю”. Направить “Инструкцию по визуальному и измерительному контролю” в Министерство юстиции Российской Федерации на государственную регистрацию. Начальник Госгортехнадзора России В.М.Кульечев Зарегистрировано в Минюсте РФ 20 июня 2003 г. Регистрационный N 4782 Инструкция по визуальному и измерительному контролю (утв. Постановлением Госгортехнадзора РФ от 11 июня 2003 г.
N 92) Настоящей Инструкции присвоен шифр РД 03-606-03. Область применения. Термины и определения III. Общие положения. Квалификация персонала.
Требования к средствам визуального и измерительного контроля. Требования к выполнению визуального и измерительного контроля VII. Оценка результатов контроля VIII. Регистрация результатов контроля. Требования безопасности Приложение А. Термины и определения основных понятий Приложение Б. Требования к содержанию “Программы (плана, инструкции) входного контроля” Приложение В.
Требования к содержанию “Технологической карты визуального и измерительного контроля” Приложение Г. Требования к содержанию “Карты операционного контроля” Приложение Д. Примерный перечень средств визуального и измерительного контроля Приложение Е. Размерные показатели для норм оценки качества по результатам визуального и измерительного контроля Приложение Ж. Формы документов, оформляемых по результатам визуального и измерительного 7контроля I.
Область применения Настоящая инструкция устанавливает порядок проведения визуального и измерительного контроля основного материала (далее материала) и сварных соединений (наплавок) при изготовлении, строительстве, монтаже, ремонте, реконструкции, эксплуатации, техническом диагностировании (освидетельствовании) технических устройств и сооружений, применяемых и эксплуатируемых на опасных производственных объектах, подконтрольных Госгортехнадзору России. Визуальный и измерительный контроль специальных материалов (например, композитных и полимерных) и специальных сварных соединений (например, муфтовой сварки) технических устройств и сооружений проводят в соответствии с требованиями специально разработанной документации. Термины и определения Настоящая инструкция базируется на терминах и определениях, приведенных в правилах безопасности, утвержденных Госгортехнадзором России (далее Правилах), а также использует термины и определения, приведенные в приложении А. Визуальный и измерительный контроль изготовления деталей и сборочных единиц, подготовки их к сборке и сварке выполняют с целью подтверждения соответствия качества их изготовления и подготовки требованиям рабочих чертежей, технологии изготовления (технологии сборки, гиба и прочей производственно-технологической документации (далее ПТД), требованиям нормативной технической документации (далее НД), ТУ на изготовление и Правил. Визуальный и измерительный контроль при сборке свариваемых элементов (заготовок, полуфабрикатов, деталей) проводят с целью выявления и проверки обеспечения допустимых размеров зазоров, смещений кромок, формы и размеров кромок и геометрического положения (излома или перпендикулярности) осей и поверхностей собранных элементов. Визуальный и измерительный контроль качества сварных соединений (наплавок) в процессе сварки (наплавки) и готового сварного соединения (наплавки) выполняют с целью подтверждения их соответствия требованиям конструкторской документации, ПТД и/или НД и Правил.
Визуальный и измерительный контроль выполненных сварных соединений (конструкций, узлов) проводят с целью выявления деформаций, поверхностных трещин, подрезов, прожогов, наплывов, кратеров, свищей, пор, раковин и других несплошностей и дефектов формы швов; проверки геометрических размеров сварных швов и допустимости выявленных деформаций, поверхностных несплошностей и дефектов формы сварных швов. Визуальный и измерительный контроль качества исправления дефектных участков в материале, сварных соединениях и наплавках выполняют с целью подтверждения полноты удаления дефекта, проверки соответствия формы и размеров выборки дефектного участка и качества заварки выборок (в случаях, когда выборка подлежит заварке) требованиям ПТД, НД и Правил. Визуальный и измерительный контроль технических устройств и сооружений в процессе эксплуатации проводят с целью выявления изменений их формы, поверхностных дефектов в материале и сварных соединениях (наплавках), образовавшихся в процессе эксплуатации (трещин, коррозионных и эрозионных повреждений, деформаций и пр.).
Визуальный и измерительный контроль при изготовлении (строительстве, монтаже, ремонте и реконструкции) технических устройств и сооружений выполняют в соответствии с требованиями Технологической карты контроля и (или) Карт (схем) операционного контроля (приложения В, Г). В указанных картах приводятся контролируемые параметры, последовательность контроля, объемы контроля, средства контроля, схемы выполнения замеров контролируемых параметров и нормы оценки результатов контроля.
Технологические карты и карты операционного контроля разрабатываются организацией, выполняющей контроль, либо специализированной организацией, выполняющей проектно-технологическую подготовку производства работ по контролю. Примечание: Допускается разработку настоящих документов производить в составе ПТД. Визуальный и измерительный контроль при оценке состояния материала и сварных соединений в процессе эксплуатации технических устройств и сооружений выполняют в соответствии с требованиями руководящих документов (методических указаний) по оценке (экспертизе) конкретных технических устройств и сооружений. При этом визуальный и измерительный контроль может выполняться в соответствии с Картами (схемами) визуального и измерительного контроля, которые разрабатываются в составе Программы технического диагностирования (освидетельствования).
В картах (схемах) указываются места проведения контроля на конкретном техническом устройстве, сооружении, схемы контроля, средства измерения контролируемого параметра, нормы оценки качества, приводятся бланки регистрации результатов контроля. Визуальный и измерительный контроль следует проводить всех доступных для этого поверхностей полуфабрикатов, заготовок, деталей, сборочных единиц, изделий. Визуальный и измерительный контроль проводят невооруженным глазом и (или) с применением визуально-оптических приборов до 20-кратного увеличения (луп, микроскопов, эндоскопов, зеркал и др.). При контроле материала и сварных соединений (наплавок) при изготовлении (строительстве, монтаже, ремонте и реконструкции) технических устройств и сооружений используют лупы с 2-7 кратным увеличением, а при оценке состояния технических устройств и сооружений в процессе их эксплуатации – лупы до 20-кратного увеличения. Визуальный и измерительный контроль выполняют до проведения контроля материалов и сварных соединений (наплавок) другими методами неразрушающего контроля, а также после устранения дефектов. Поверхности материалов и сварных соединений (наплавок) перед контролем очищаются от влаги, шлака, брызг металла, ржавчины и других загрязнений, препятствующих проведению контроля. Измерения проводят после визуального контроля или одновременно с ним.
Измерения деталей, подготовленных под сварку, проводятся до их сборки. Визуальный и измерительный контроль материалов, сварных соединений (наплавок), подлежащих термической обработке, производят до и после указанной операции. Если контролируемая деталь, конструкция или узел подлежит полной термической обработке (нормализации или закалке с последующим отпуском), контроль проводят после ее выполнения.
Визуальный и измерительный контроль материалов и сварных соединений, подлежащих механической обработке, в том числе с удалением валика усиления шва, или деформированию, проводят до и после указанных операций.
Инструкция устанавливает обязательные требования к организации и порядку производства работ по визуальному и измерительному контролю, включая требования к подготовке и аттестации персонала, средствам контроля, организации работ, фиксации результатов контроля и т.д. При изготовлении, монтаже, ремонте, реконструкции и эксплуатации оборудования, металлических конструкций и трубопроводов энергетических объектов, на которые распространяется действие нормативно-технических документов Госгортехнадзора России, Госатомнадзора России и Минстроя России. Действует РД 03-606-03, утв.
Постановлением № 92 Госгортехнадзора России. РУКОВОДЯЩИЙ ДОКУМЕНТ РД 34.10.130-96 ИНСТРУКЦИЯ ПО ВИЗУАЛЬНОМУ и ИЗМЕРИТЕЛЬНОМУ КОНТРОЛЮ МОСКВА 1996 МИНИСТЕРСТВО ТОПЛИВА И ЭНЕРГЕТИКИ РОССИЙСКОЙ ФЕДЕРАЦИИ АТТЕСТАЦИОННЫЙ НАУЧНО-ТЕХНИЧЕСКИЙ ЦЕНТР «ЭНЕРГОМОНТАЖ» СОГЛАСОВАНО УТВЕРЖДАЮ Госгортехнадзор России Письмо № 12-22/357 от г. Заместитель министра топлива и энергетики Российской Федерации Госатомнадзор России Письмо № 14-20/119 от г.
Кудрявый «15» августа 96 г. РУКОВОДЯЩИЙ ДОКУМЕНТ ИНСТРУКЦИЯ ПО ВИЗУАЛЬНОМУ и ИЗМЕРИТЕЛЬНОМУ КОНТРОЛЮ РД 34.10.130-96 СОГЛАСОВАНО Начальник департамента Энергореновации РАО «ЕЭС России» В.А. Стенин «29» 07 96 г. РАЗРАБОТЧИК АНТЦ «Энергомонтаж» Генеральный директор В.Б. Богод «29» июля 96 г. Начальник департамента реновации и технического перевооружения корпорации «ЕЭЭК» В.Е. Азерников «30» 07 96 г.
Руководитель работы С.A. Белкин «25» июля 96 г. Директор дирекции по технической экспертизе корпорации «ЕЭЭК» Ю.И. Гусев «31» 07 1996 г. Группа В09 Руководящий документ Инструкция по визуальному и измерительному контролю РД 34 10.130-96 Дата введения 1996-01-07 Настоящая инструкция устанавливает обязательные требования к организации и порядку производства работ по визуальному и измерительному контролю, включая требования к подготовке и аттестации персонала, средствам контроля, организации работ, фиксации результатов контроля и т.д.
Тип Назначение Конструктивное исполнение Группа лупы Оптическая система ЛП Для просмотра деталей, мелких предметов и т.д. Тип прибора, инструмента Марка ГОСТ, ТУ Код ОКП Документа поверку Диапазон измерений Цена деления, мм Допускаемая погрешность измерений, мм Габариты, мм Масса, кг Изготовитель 1 2 3 4 5 6 7 8 9 10 11 Профилограф-профилометр Мод. 280 ТУ 2.03423- 1122 280.000.0. ООПС Профилограф 0,02-100 мкм Датчик 16´70´180 0,02 Московский инструментальный завод «Калибр» Профилометр Ra-0,02-25 мкм Привод 28´48´112 0,4 Rz-0,2-100 мкм Электронный блок 220´205´75 2,0 Rp-0,1-50 мкм Rv-0,1-50 мкм Прибор записывающий 112´240´70 2,5 Rmax-0,2-100 мкм Образцы шероховатости поверхности (сравнения) (СТ СЭВ 848) Угломер с нониусом УН 39 4411 0-180 град 2 мин ± 2 мин То же мод. Контролируемый параметр Место контроля Требования по контролю 1. Наружный диаметр (Dн); внутренний диаметр (Dв) Измерительный Измерение Dн и Dв с обоих концов трубы. Измерение Dв производится при поставке труб по внутреннему диаметру 2.
Толщина листа, стенки трубы (Sн) то же Измерение Sн с обоих концов трубы не менее, чем в двух точках. Измерение Sн листа не менее, чем в двух точках (по длине, ширине) с каждой стороны листа 3. Овальность трубы (а) то же Измерение размера «а» с обоих концов трубы 4. Кривизна трубы (б) то же Измерение кривизны на участке 1 м в двух сечениях по длине 5.
Длина трубы, листа (L) то же Измерение не менее 3 труб от партии 6. Ширина листа (В) то же Измерение не менее 3 листов от партии 7. Трещины, плены, рванины, закаты, раковины, расслоения Визуальный Осмотр наружной поверхности невооруженным глазом; осмотр внутренней поверхности труб невооруженным глазом (при наличии доступа) и с помощью перископа, эндоскопа и пр. Разрешается вырезка контрольных образцов длиной 200 мм в количестве не менее 2 шт. И их осмотр после разрезки Примечания: 1) Контролю по п.
1.4 подлежат не менее 50% труб (листов) от партии. 2) Контролю по п. 7 подлежит не менее 10% длины каждой трубы (площади поверхности листа).
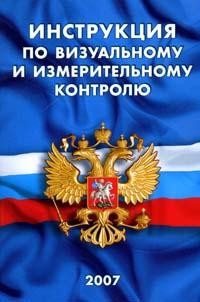
4.4 Порядок выполнения визуального и измерительного контроля подготовки и сборки деталей под сварку. Контролируемый параметр Условное обозначение (рис. 1) Рисунок Средства измерений. Требования к измерениям 1 2 3 4 1.
Угол скоса кромки a, b, a 1 1a, б, г, д, е, k Угломер или шаблон универсальный. Измерение в одном месте 2. Притупление кромки р, р 1 1a, б, г, д, е Штангенциркуль ШЦ-1. Измерения в двух взаимоперпендикулярных сечениях (4 точки) 3. Ширина «уса» разделки или скоса кромки с 1 б, е, т Штангенциркуль ШЦ-1. Измерения в трех точках равномерно по длине (периметру).
Глубина скоса кромки М 1д, k 1, у Штангенциркуль ШЦ-1, линейка. Измерение не менее, чем в трех точках по длине. Высота присадочного выступа h в 1ж Штангенциркуль ШЦ-1. Измерения в двух взаимоперпендикулярных сечениях (4 точки) 6.
Длина расточки (раздачи) труб по внутреннему диаметру l р 1з То же 7. Угол выхода резца (калибра) g 1з, и Шаблон универсальный или угломер. Измерение в одном месте 8. Диаметр расточки D p Штангенциркуль ШЦ-1.
Измерение в двух взаимоперпендикулярных сечениях (4 точки). Толщина стенки в месте расточки S p 1з, и Штангенциркуль ШЦ-1. Измерения не менее, чем в трех точках равномерно по длине 10. Эмулятор windows phone 8 на пк.
Ширина подкладного кольца В к 1л, м, н Штангенциркуль ШЦ-1. Измерения не менее, чем в трех точках по длине (периметру). Толщина подкладного кольца S к 1л, м, н То же 12. Притупление подкладного кольца р к 1л, м, н То же 13. Диаметр расплавляемого кольца (вставки) D к, D вс 1л, м, н, о Штангенциркуль ШЦ-1. Измерения в двух взаимоперпендикулярных сечениях (4 точки) 14. Высота расплавляемого кольца (вставки) A 1о Штангенциркуль ШЦ-1.
Измерения не менее, чем в трех точках равномерно по периметру 15. Ширина расплавляемого кольца (вставки) В вс 1о То же 16. Длина сектора отвода (сварного) по наружной образующей H 1п Линейка. Измерение детали в зоне максимального размера 17. Длина сектора отвода (сварного) по внутренней образующей Р 1п Линейка. Измерение детали в зоне минимального размера 18.
Угол наклона кромки сектора отвода (сварного) a 2 1п Линейка и угломер или шаблон универсальный. Измерять скос кромки с обоих сторон (a 2 = 0,5 a 2 + 0,5 a 2) 19. Отклонение торца разделки (трубы) от перпендикуляра к образующей трубы f 1п Угольник и щуп. Измерения не менее, чем в трех сечениях в зоне максимального смещения. Либо: отвес и линейка или щуп 20. Диаметр отверстия в корпусе (трубе) d 1с, т, у Штангенциркуль ШЦ-1. Измерения в двух взаимоперпендикулярных сечениях (4 точки) 21.
Диаметр расточки в корпусе (трубе) d 1 1у То же 23. Шероховатость зачищенных поверхностей Профилограф-профилометр, образцы шероховатости (сравнения). Контролируют поверхности, указанные в п.
4.2.6 Примечание - Допускаются другие способы и средства измерений, обеспечивающие достоверность контроля параметра подготовки деталей под сварку. Таблица 7 - Требования к измерениям размеров сборки соединений деталей под сварку. Контролируемый параметр Условное обозначение (рис. 2) Номер рисунка Средства измерений.
Требования к измерениям 1 2 3 4 1. Зазор в соединении а 2б, в, г, д, е Щуп, шаблон универсальный. Измерение - см. Смещение кромок деталей с внутренней стороны соединения b 2а Линейка и щуп.
Измерение - см. Смещение кромок деталей с наружной стороны соединения F 2а, б Линейка и щуп. Измерение - см. Зазор между подкладным кольцом и внутренней поверхностью детали b 1 2б Шаблон специальный.
Измерения не менее, чем в трех точках по длине (периметру) соединения 5. Смещение проволочной вставки с внутренней стороны b 2 2б Штангенциркуль ШЦ-1, шаблон универсальный или щуп. Измерение выполняется после прихватки вставки к кромке разделки одной из деталей 6. Зазор в замке расплавляемого кольца (вставки) a 1 - Шаблон универсальный или щуп. Измерение выполняется после прихватки вставки к одной из деталей 7. Несимметричность штуцера б 2 2ж Контрольный стенд специальный.
Измерение согласно п. Расстояние приварного элемента крепления от кромки разделки С 2з Линейка. Измерению подлежит каждый элемент крепления 9. Катет шва приварки элемента крепления К 2з Линейка и щуп, штангенциркуль ШЦ-1, шаблон. Измерению подлежит каждый шов 10. Перелом осей цилиндрических элементов и угловое смещение поверхностей листов k 2и Линейка (L = 400 мм) и щуп. Измерение - см.
Длина прихватки l n 2к Линейка или штангенциркуль ШЦ-1. Измерение каждой прихватки. Высота прихватки h n 2к Штангенциркуль ШЦ-1. Измерение каждой прихватки 13. Расстояние между прихватками L n 2к Линейка. Измерение расстояния между прихватками соединения выполняется в случаях, когда расстояние между прихватками регламентируется ПТД 4.4.8 Измерительный контроль величины зазора в соединении, величины смещения кромок и перелома плоскостей в соединениях выполнять не реже, чем через один метр по длине соединения, но не менее, чем в трех сечениях, равномерно расположенных по длине шва.
При невозможности (отсутствие доступа) контроля смещения кромок с внутренней стороны соединения оценку возможного смещения следует производить по смещению наружных кромок деталей (размер F) либо по смещению притупления «усов» V-образной разделки (см. 1б, размер р). 4.4.9 Замеры, в первую очередь, следует выполнять на участках, вызывающих сомнение в части размеров по результатам визуального контроля. 4.4.10 При визуальном и измерительном контроле размеров и качества прихваток контролю подлежит каждая прихватка в соединении.
4.4.11 Измерения швов приварки временных технологических креплений и расстояния от приварного элемента крепления до кромки разделки выполняют в одном месте. Контролю подлежит каждое крепление и каждый шов крепления. 4.4.12 Перелом осей, собранных под сварку кольцевых соединений цилиндрических элементов, выполняется в 2-3 сечениях (в зоне максимального излома, выявленного при визуальном контроле) на расстоянии 200 мм от центра соединения. При отсутствии прямолинейного участка детали длиной 200 мм разрешается измерение размера производить на участке меньшей длины с последующим перерасчетом к длине 200 мм по формуле: где k 1 и L - размер перелома осей и расстояние от соединения, на котором выполнено измерение (рис. Рисунок 3 - Схема измерения перелома осей цилиндрических элементов 4.4.13 Несимметричность штуцера в поперечном сечении определяется путем выполнения не менее двух измерений в одном сечении.
Разрешается выполнять контроль несимметричности отверстия под штуцер на стадии контроля подготовки деталей под сварку. 4.4.14 Схемы измерения отдельных размеров подготовки деталей под сварку и сборки соединений под сварку с помощью шаблона универсального типа УШС приведены на рис. Рисунок 4 - Шаблон универсальный типа УШС Рисунок 5 - Схема измерения угла скоса разделки Рисунок 6 - Схема измерения размера притупления разделки Рисунок 7 - Схема измерения зазора в соединении Рисунок 8 - Схема измерения смещения наружных кромок деталей 4.5 Порядок выполнения визуального и измерительного контроля сварных соединений (наплавок) 4.5.1 Визуальный и измерительный контроль сварных соединений выполняется при производстве сварочных работ (послойный контроль в процессе сварки с фиксацией результатов контроля) и на стадии приемо-сдаточного контроля готовых сварных соединений. Послойный контроль в процессе сварки выполняется в случаях, например, невозможности проведения неразрушающих методов контроля или в случаях, оговоренных в рабочих чертежах при согласовании с Заказчиком и головной материаловедческой организацией (последнее - для объектов атомной энергетики). 4.5.2 Визуальный послойный контроль в процессе сварки соединения выполняется с целью подтверждения отсутствия недопустимых поверхностных дефектов (трещин, пор, включений, прожогов, свищей, усадочных раковин, несплавлений, грубой чешуйчатости, западаний между валиками, наплывов) в каждом слое (валике) шва. Выявленные при контроле дефекты подлежат исправлению перед началом сварки последующего слоя (валика) шва.
Сварные соединения, выполненные с послойным визуальным контролем, подлежат дополнительно контролю капиллярной или магнитопорошковой дефектоскопией на доступных участках. Контролируемый параметр Условное обозначение (рис. 9) Номер рисунка Средства измерений. Требования к измерениям 1. Ширина шва е, e 1 9a, б Штангенциркуль ШЦ-1 или шаблон универсальный.
Измерение - см. Высота шва g, g 1 9a, б То же 3. Выпуклость обратной стороны шва g 1 9a Штангенциркуль ШЦ-1.
Измерение согласно п. Вогнутость обратной стороны шва g 2 9б Штангенциркуль ШЦ-1, в т.ч.
Инструкция По Визуальному И Измерительному Контролю Скачать Бесплатно
Модернизированный (рис. Измерения в 2-3 местах в зоне максимальной величины 5. Глубина подреза (неполного заполнения разделки) b 2, b 3 9r Штангенциркуль ШЦ-1, в т.ч.
Модернизированный (рис. Измерение согласно п. Катет углового шва К, K 1 1г, д Штангенциркуль ШЦ-1 или шаблон. Измерение согласно п. Чешуйчатость шва D 1 1ж Штангенциркуль ШЦ-1, в т.ч. Модернизированный (рис. Измерения не менее, чем в 4 точках по длине шва 8.
Глубина западаний между валиками D 2 1з То же 9. Размеры (диаметр, длина, ширина) одиночных несплошностей d g, l g, b g 1и Лупа измерительная. Измерению подлежит каждая несплошность Рисунок 9 - Размеры сварного шва, подлежащие измерительному контролю. А) и б) размеры (ширина, высота) стыкового одностороннего шва с наружной и внутренней стороны; в) то же двухстороннего сварного шва, г) подрез или неполное заполнение разделки кромок; д) чешуйчатость (D 1) шва и западание между валиками шва (D 2); е) размеры поверхностных включений (диаметр - d g, длина - l g, ширина - b g, включения); ж) размеры катета шва таврового (углового, нахлесточного) соединения.
4.5.5 Высота и ширина сварного шва должна определяться не реже, чем через один метр по длине соединения, но не менее, чем в трех сечениях равномерно расположенных по длине шва. При контроле стыковых сварных соединений труб наружным диаметром до 89 мм включительно с числом однотипных соединений более 50 на одном изделии допускается определение размеров шва выполнять на 10-20% соединений в одном-двух сечениях, при условии, что при визуальном контроле, которому подвергают все соединения, нет сомнений в части размеров (ширина, высота) шва.
4.5.6 При измерительном контроле наплавленного антикоррозионного покрытия замеры его толщины на цилиндрических поверхностях проводить не реже, чем через 0,5 м в осевом направлении и через каждые 60° по окружности при ручной наплавке и 90° при автоматической наплавке. На плоских и сферических поверхностях проводят не менее одного замера на каждом участке размером 0,5 м ´ 0,5 м (длина ´ ширина) при автоматической наплавке. 4.5.7 При контроле угловых сварных соединений определяют катеты сварного шва. Определение высоты, выпуклости и вогнутости углового шва выполняется только в тех случаях, когда это требование заложено в рабочих чертежах. Измерение выпуклости и вогнутости производится с помощью специальных шаблонов, а определение высоты углового шва расчетным путем. 4.5.8 Измерение глубины западаний между валиками при условии, что высоты валиков отличаются друг от друга, должно выполняться относительно валика, имеющего меньшую высоту. Аналогично определять и глубину чешуйчатости валика (по меньшей высоте двух соседних чешуек).
4.5.9 Измерения размеров, указанных в п. 4.5.5.4.5.8 и таблице 8, выполняют в первую очередь на участках шва, вызывающих сомнение в части размеров по результатам визуального контроля. 4.5.10 Выпуклость (вогнутость) стыкового шва оценивается по максимальной высоте (глубине) расположения поверхности шва от уровня расположения наружной поверхности деталей. В том случае, когда уровни поверхности деталей одного типоразмера (диаметр, толщина) отличаются друг от друга, измерения следует проводить относительно уровня поверхности детали, расположенной выше уровня поверхности другой детали (рис. В том случае, когда выполняется сварка деталей с различной толщиной стенки и уровень поверхности одной детали превышает уровень поверхности второй детали, оценку выпуклости (вогнутости) поверхности шва выполнять относительно линии, соединяющей края поверхности шва в одном сечении (рис. 12) с помощью специального шаблона. 1 - штангенциркуль 2 - опора Рисунок 10 - Штангенциркуль типа ШЦ-1 с опорой Рисунок 11 - Схема измерения высоты шва стыкового соединения при различном уровне наружных поверхностей деталей, вызванном смещением при сборке соединения.
4.5.11 Выпуклость (вогнутость) углового шва оценивается по максимальной высоте (глубине) расположения поверхности шва от линии, соединяющей края поверхности шва в одном поперечном сечении (рис. 4.5.12 Размеры выпуклости (вогнутости) стыкового (рис.
12) и углового (рис. 13) швов определяются специальными шаблонами. Рисунок 12 - Схема измерения высоты шва стыкового соединения при различном уровне наружных поверхностей деталей, вызванном разницей в толщинах стенок. Рисунок 13 - Схема измерения выпуклости (g) и вогнутости (g 3) наружной поверхности и высоты (h) углового шва. Рисунок 14 - Схема измерения выпуклости (g 1) и вогнутости (g 2) обратной стороны стыкового одностороннего шва. 4.5.13 Выпуклость (вогнутость) корня шва оценивается по максимальной высоте (глубине) расположения поверхности корня шва от уровня расположения внутренних поверхностей сваренных деталей. В том случае, когда уровни внутренних поверхностей разные, измерения следует проводить согласно схемы, приведенной на рис.
4.5.14 Схемы измерения отдельных размеров сварного соединения с помощью шаблона универсального типа УШС приведены на рис. Рисунок 15 - Схема измерения с помощью шаблона УШС размеров сварного шва а) измерение высоты шва и глубины подреза; б) измерение ширины шва; в) измерение западаний между валиками 4.5.15 Измерения чешуйчатости и западаний между валиками шва, глубины и высоты углублений (выпуклостей) в сварном шве и основном металле, в т.ч. При техническом диагностировании, разрешается определять по слепку, снятому с контролируемого участка. Материалом для слепка могут служить пластилин, воск, гипс и другие материалы. Измерения проводят с помощью измерительной лупы или на микроскопе после разрезки слепка механическим путем.
4.5.16 Измерения перелома осей цилиндрических элементов и угловое смещение плоскостей плоских деталей, а также несимметричности штуцера выполнять при контроле сварных узлов и деталей (см. 4.6.9 и 4.6.10). 4.6 Порядок выполнения визуального и измерительного контроля сварных узлов и деталей 4.6.1 Визуальный контроль сварных узлов и деталей предусматривает проверку: отклонений по взаимному расположению элементов сварного узла; наличия маркировки сварных соединений; наличия маркировки узла (детали); отсутствия поверхностных повреждений материала, вызванных отклонениями в технологии изготовления, транспортировкой и условиями хранения; наличия окраски поверхностей; отсутствия неудаленных приварных элементов (технологические крепления, гребенки, бобышки). 4.6.2 Измерительный контроль гнутых колен труб предусматривает проверку: отклонения от круглой формы (овальность) в любом сечении гнутых труб (колен); толщины стенки в растянутой части гнутого участка трубы (колена); радиуса гнутого участка трубы (колена); высоты волнистости (гофры) на внутреннем обводе гнутой трубы (колена); неровностей (плавных) на внешнем обводе (в случаях, установленных НТД); предельные отклонения габаритных размеров.
(предприятие, организация) АКТ № от визуального и/или измерительного контроля 1. (предприятие, организация) АКТ № от визуального и/или измерительного контроля качества сварных швов в процессе сварки соединения (наименование изделия и номер соединения) 1. Настоящим актом удостоверяется факт выполнения сварщиком (фамилия, и.о., клеймо) (углового, стыкового) соединения (см. Сварочный формуляр), выполненного (указать способ сварки и положение) в соответствии с требованиями технологии сварки (указать и недоступного для контроля шифр технологии) (указать способ контроля, предписанный конструкторской документацией) 2. Обозначение НТД и ПТД Наименование Государственные стандарты Нутромеры микрометрические.
Технические условия Штангенрейсмасы. Технические условия Штангенциркули. Технические условия Линейки измерительные металлические.
Образец письма в центр занятости. Технические условия Нутромеры индикаторные с ценой деления 0,01 мм. Технические условия Меры плоского угла призматические. Общие технические условия Угольники поверочные 90°. Технические условия Наборы принадлежностей к плоскопараллельным мерам длины. Технические условия Угломеры с нониусом.
Технические условия Эмаль ПФ-115. Технические условия Микрометры. Технические условия Эмали НЦ-5123. Технические условия Рулетки измерительные металлические. Технические условия Меры длины концевые плоскопараллельные.
Технические условия Образцы шероховатости поверхности (сравнения). Общие технические условия Толщиномеры и стенкомеры индикаторные с ценой деления 0,01 мм и 0,1 мм. Технические условия Меры длины штриховые брусковые. Технические условия Нутромеры микрометрические. Методы и средства поверки Средства измерения шероховатости поверхности профильным методом. Профилографы-профилометры контактные.
Типы и основные параметры Картон термоизоляционный прокладочный. Технические условия Контроль неразрушающий. Методы оптического вида.
Общие требования Входной контроль продукции. Основные положения Лупы. Типы, основные параметры. Общие технические требования Клейма ручные буквенные и цифровые. Типы и основные размеры ЕСКД.
Правила внесения изменений ГСИ. 1 Общие положения. 2 2 Требования к персоналу.
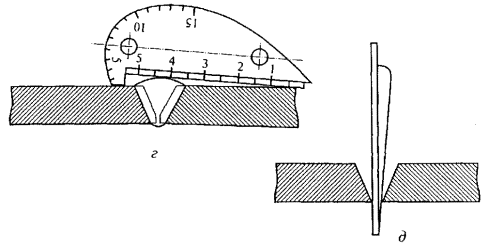
5 3 Требования к приборам и инструментам для визуального и измерительного контроля. 6 4 Требования к выполнению визуального и измерительного контроля. 11 4.1 Подготовка мест производства работ. 11 4.2 Подготовка объектов к контролю. 11 4.3 Порядок выполнения визуального и измерительного контроля основного материала. 12 4.4 Порядок выполнения визуального и измерительного контроля подготовки и сборки деталей под сварку.
14 4.5 Порядок выполнения визуального и измерительного контроля сварных соединений (наплавок) 21 4.6 Порядок выполнения визуального и измерительного контроля сварных узлов и деталей. 25 4.7 Порядок выполнения визуального и измерительного контроля при исправлении дефектов в основном материале и сварных соединениях изделий. 27 4.8 Порядок выполнения визуального и измерительного контроля при техническом диагностировании. Оценка результатов контроля.
Регистрация результатов контроля. Требования безопасности. 30 Приложение А Термины и определения основных понятий.
30 Приложение Б Требования к содержанию «Программы (плана, инструкции) входного контроля материала (полуфабриката) или изделия». 42 Приложение В Требования к содержанию «Технологической карты визуального и измерительного контроля».
43 Приложение Г Требования к содержанию «Карты операционного контроля». 44 Приложение Д Программа подготовки специалистов к аттестации на право выполнения работ и руководства работами по визуальному и измерительному контролю. 44 Приложение Е Формы документов, оформляемых по результатам визуального и измерительного контроля. 49 Приложение Ж Клеймение деталей, сборочных единиц и сварных соединений.
Руководящий Документ. Инструкция По Визуальному И Измерительному Контролю
51 Информационные данные.